In the entire import and export trade process, each country has different access requirements, but whether it is products or documents, they must meet compliance requirements, otherwise many problems will arise, and in serious cases, both money and goods will be lost. Of course, we are willing to use our professional knowledge and experience to provide you with ideas for solving problems, and we will also assist you in solving problems together.
Cross-border sourcing offers opportunities but comes with risks, including compliance challenges, quality inconsistencies, cultural misunderstandings, and delivery delays. Non-compliance with trade regulations or certifications can lead to severe penalties, confiscated shipments, and reputational harm. Addressing these risks requires a reliable partner who can navigate complex requirements, resolve disputes swiftly, and safeguard your business’s success.
Therefore, a professional who is always with you and has the ability to solve problems is crucial to the stability and success of your business!
What should we do to avoid it?
Principle: Prevent problems before they occur and solve them promptly after they occur.
Preventing invisible problems
Solve problems that have already occurred
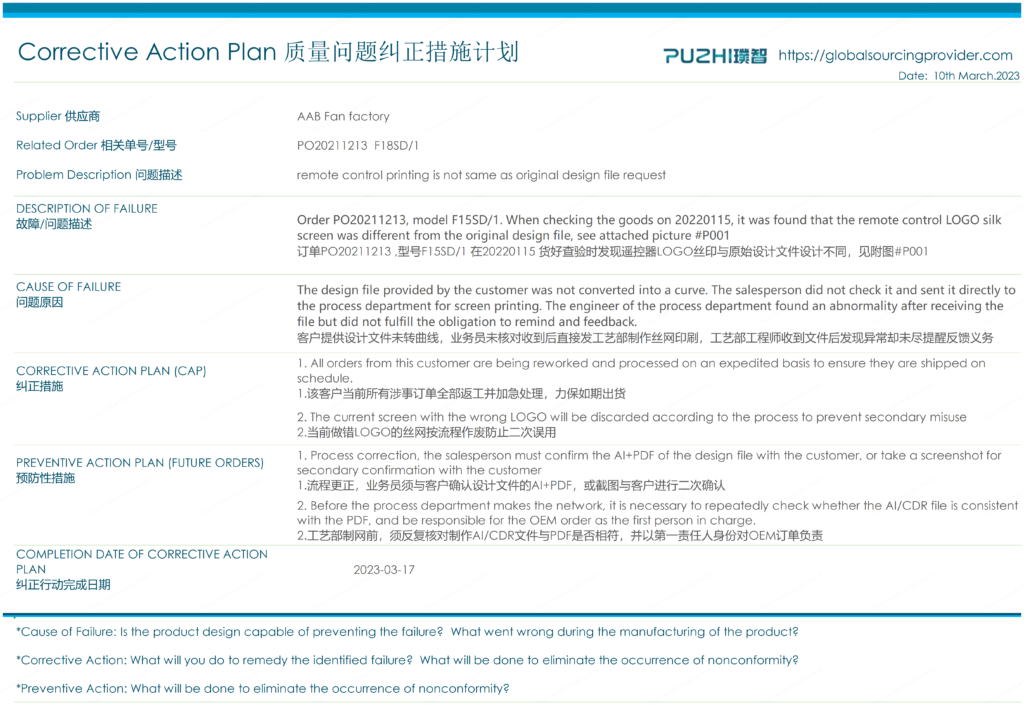